Munich, December 16, 2021 | Did you ever wonder how it’s possible that spare parts for foreign cars are often delivered to a workshop within only a few days? Of course, there has to be some secret behind that. Let’s take a look at the well-oiled machine that is modern parts supply, and let us show you how we do it.
Supply Chain Management is crucial to almost any industry, especially when that industry involves cars and the thousands of parts they are made of. AEC offers automotive solutions, so we don’t only focus on bringing foreign cars to new markets, but also on the care and maintenance they need afterward. Of course, spare parts are a vital part of any maintenance or repair work that’s done over the lifespan of a vehicle. Some parts simply need to be replaced every now and then. This is sometimes foreseeable – in the case of regularly scheduled maintenance – and sometimes unforeseeable and spontaneous – for when a car gets into an accident and needs to be brought back on the road as soon as possible.
As you can see, the requirement for parts is simple: They need to be in the right place at the right time.
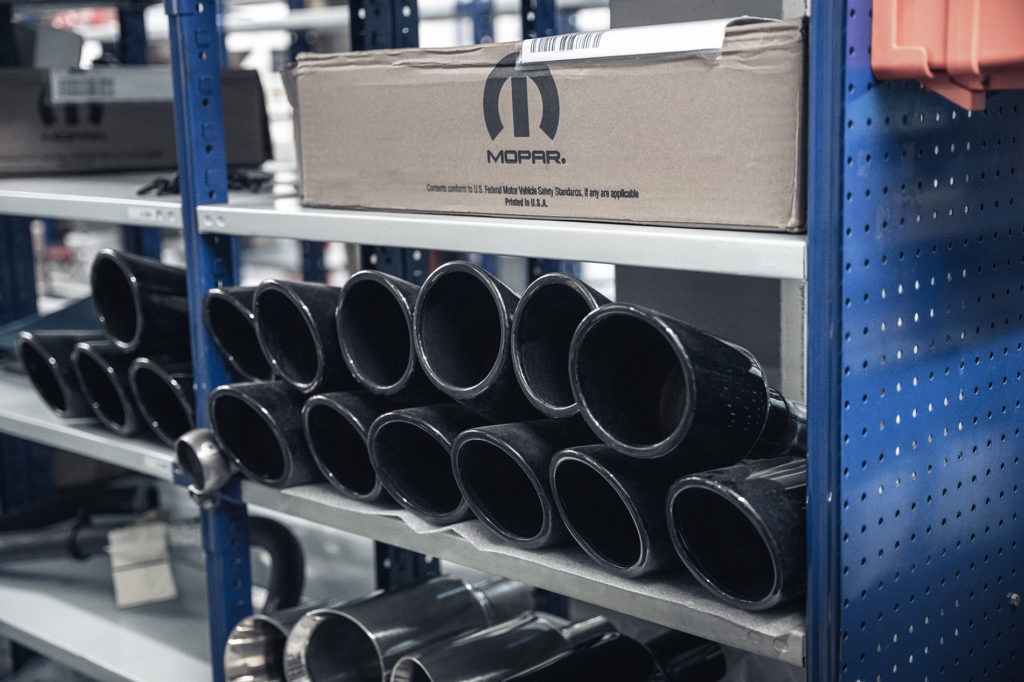
At first glance, this may seem straightforward, but every single part of our huge catalog of almost one million items is used in a different frequency. To put it simply: You will have to change your brake pads a lot more often than your engine, so it probably makes more sense to stock more brake pads than engines, right?
Imagine that one of the vehicles we offer requires the replacement of a specific spare part at every maintenance service – a typical wear item, like a gasket or a particular bolt type. Our dealerships all over Europe and other parts of the world need a steady supply of this wear item every week or month for their workshops, where it’s used on almost every car. It wouldn’t be very efficient to have this part delivered from the other end of the world every time, would it?
Therefore, we keep a large amount of those parts in stock at our AEC warehouse facilities near the port of Antwerp. They can quickly be delivered in any number, and all over Europe within two or three days, sometimes within hours, using express delivery.
Other items like body parts however are rarely needed at all. They only need to be replaced when they are damaged. And then a bumper would be needed more often than a roof skin for example. This is where a smaller number of parts is in stock, and possibly longer wait times may occur.
However, an unexpected factory recall may create a sudden demand for a part that was barely needed before. You can see there are a plethora of factors that need to be managed optimally.
This all breaks down to Supply Chain Management. In any field of business, the supply chain itself is nothing more than the logistics processes that an item goes through on the way from its production to its delivery. However, on that way, every resource needs to be delivered where it is needed at the exact right time. That’s especially crucial if those resources come from an external supplier.
Here is another example: Think of a car factory. It needs a steady supply of tires. They can’t be produced on-site, and there’s no space to store huge stock of tires. They would be depleted too quickly anyway. Logically, the tires come from a tire factory. Every new car meets its set of wheels just before it rolls off the assembly line. Just before that, in another part of the factory, the tires are mounted onto the correct rims. Too many tires would cause a pile-up. Not enough tires would result in a halted production – not good at all!
Tiny but crucial details like this form the links of every supply chain – no matter if a workshop orders a spare bolt or a carsharing provider needs an entire fleet of vehicles, delivered just in time. Thanks to our dedicated AEC Supply Chain Team, we have all the experience and expertise needed.
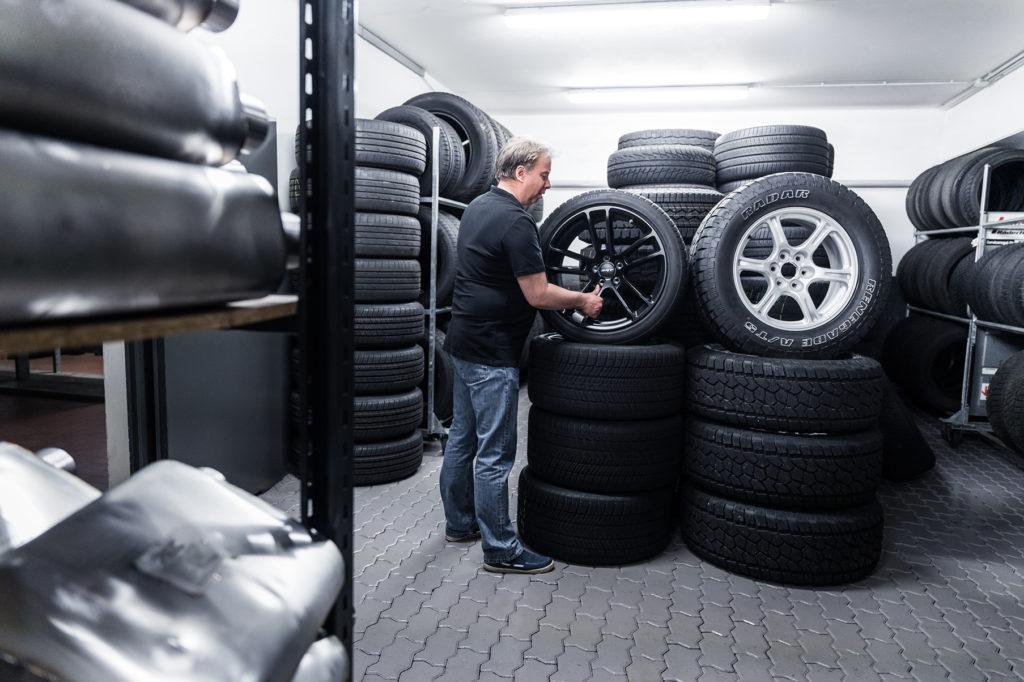
Time is money, but space is money too!
Part of their daily business consists of forecasting the need for items, ensuring correct and timely delivery, and adapting to the customer’s needs. Every operation is processed by our AEC Warehouse. Managing the storage spaces in that warehouse is another facet of Supply Chain Management. We all know the term “time is money”, but in this case, “space is money” too. If the stock of a certain part gets sold out, it leaves an open space on a shelf. What is the most economic point in time to re-stock that part? Should that space be used for a different item that will be used more frequently? Do other spaces need to be cleared for that new stock? Questions like these add up to an intricate machinery that needs to function perfectly.
Of course, we live in high-tech times, and many processes are automated. However, that is not always easy. But remember? AEC is an automotive solutions company with 25 years of experience! To process all of our parts operations, we could just make do, with an off-the-shelf warehousing software, that you would also find in a food warehouse, or a factory that makes paperclips. But in reality, car parts have huge differences. Some need to be handled with extra care, because they contain fluids or explosives, like airbags or belt tensioners do. Some parts are the size of a fingernail, while other times, huge and heavy parts on pallets need to be processed. All those items need to find the right transport outlet that is specialized in handling those goods. It’s as complicated as it is fascinating. So, we found a solution and created a system that helps us automize even the most complex supply chain matters – whether it’s a fancy racing stripe decal that you want to put on your sports car or a badge of thousands of cars that need to be delivered to a fleet company just-in-time.
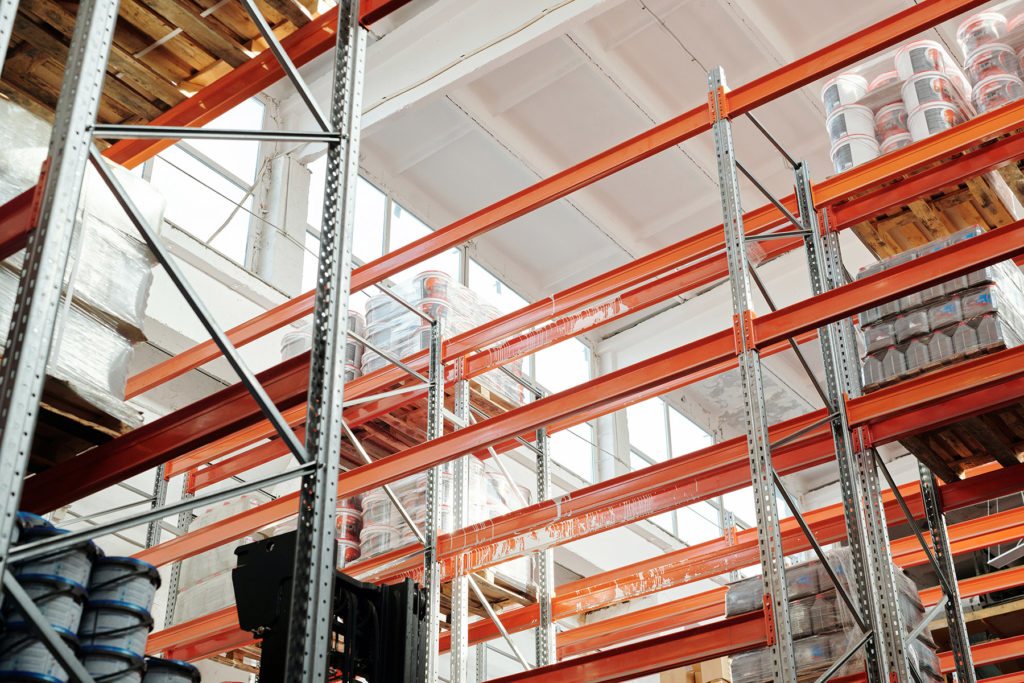
In the third and last part of our mini-series, we will look at how we can make all of this happen with our own intelligent software.
If we have raised your interest on our Parts- and Supply Chain Management at AEC, be sure to check out our career page, where we currently offer many new vacancies in this field:
https://www.aecsolutions.com/career/job-vacancies/
This article is the second part of our mini-series about Supply Chain Management. You can find the first article here: https://blog.aecsolutions.com/get-on-board-how-our-supply-chain-works-pt-1